디지털 트윈(Digital Twin) 기술은 현실 세계의 요소를 가상공간에 재현하여 분석하고 예측하는 차세대 응용 시스템이다. 이 기술은 AI, 클라우드, IoT, 빅데이터 등을 통합하여 물리적 세계를 디지털로 복제하고 이를 통해 다양한 시뮬레이션을 수행한다. 스마트 팩토리에서 이 기술을 활용하면 제품의 전주기를 통합적으로 관리하며 효율성을 극대화할 수 있다. 이에이트가 제안하는 디지털 트윈 방안은 무엇인지 ‘2024 제조혁신기술 컨퍼런스’에서 이에이트 류수영 상무가 발표한 내용을 정리했다.
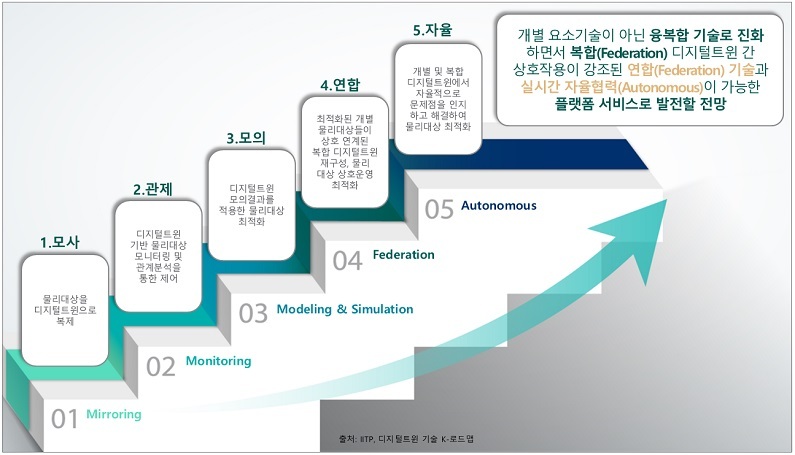
디지털 트윈(Digital Twin) 기술은 메타버스(Metaverse) 기술과 함께 몇 해 전부터 조명받기 시작했다. 현실에 존재하는 요소를 가상공간에서 구현해 활용한다는 점에서 산업 내 ‘모의시험’ 과정을 수행하고 있다.
이 기술은 인공지능(AI), 클라우드, IoT, 빅데이터 등 차세대 기술이 접목된 응용 애플리케이션 시스템이다. 결국 융합 기술로 탄생한 예측 및 분석 특화 기술인데, 물리적 세계를 디지털 세계로 복제한 후 과거와 현재를 분석하고 미래를 예측한다는 게 기술적 핵심이다. 즉 IoT 시스템, 센서 등으로 수집된 비정형 데이터를 가상세계로 녹여 상황을 분석할 수 있다.
디지털 트윈의 최대 강점은 모든 데이터를 가상공간에서 언제든 재현·분석하고, 이를 토대로 상황에 대한 대응책을 마련할 수 있다는 것이다. 미처 인지하지 못했던 상황을 다시 되돌려 검토한 후 새로운 인사이트를 도출할 수 있다.
디지털 트윈 기술발전 다섯 단계
디지털 트윈은 모사(Mirroring)·관제(Monitoring)·모의(Modeling·Simulation)·연합(Federation)·자율(Autonomous) 등 다섯 단계의 발전 과정을 거친다고 정의된다. 모사 단계에서는 물리적인 대상을 가상 환경으로 복제한다. 관제, 즉 모니터링 과정은 모사 단계의 데이터를 활용해 대시보드와 같은 형태로 구현한다. 이후 실제로 어떻게 구현되는지 시각적으로 나타내는 단계다.
세 번째 모의 단계에서는 모델링의 시뮬레이션 과정이라고 생각하면 쉽다. 각종 시뮬레이션 영역을 적용해 예측·분석하는 단계다. 그 다음 연합 단계는 모의 단계를 거친 복합 디지털 트윈이 서로 연동돼 예상치 못한 복합적인 상황에 대한 시뮬레이션이 가능하게 된다. 이는 디지털 트윈 내 객체까지도 함께 동기화돼 높은 정확도의 결과물을 도출한다. 끝으로 자율 단계는 연합 단계가 발전된 형태로, 디지털 트윈 전 과정을 자율적으로 수행하는 것을 의미한다. 자율 단계가 비로소 디지털 트윈이 최종적으로 지향하는 비전이다.
디지털 트윈은 현재 모의 단계까지 기술적 진화가 완성된 것으로 알려졌다. 이를 제조 영역 내 스마트 팩토리에 적용한다면 실시간성을 구현하는 것이 관건이 될 것이다. 이 과정에서 IoT 시스템이 강조된다. 엣지단의 설비 및 장비에서 전송되는 각종 데이터를 수집해야 되기 때문에 이 기술은 핵심적으로 필요하다.
또 3D 모델링을 빼놓을 수 없다. 설비, 제품, 부품 등을 모두 가상화해야 하고, 3D 모델링을 통해 탄생된 하나의 객체가 IoT에서 전송되는 데이터와 연계돼야 현실과 똑같은 형태의 객체가 탄생된다.
이렇게 객체가 만들어지고 구현되면, 빅데이터·AI 등을 통해 해당 객체를 분석한 후 예측 모델이 생성된다. 이후 해당 예측 모델을 활용해 예상되는 결과를 도출하고, 공정 고도화 실현에 응용한다. 예를 들어 디지털 트윈으로도 출된 예측 결과값을 생산성 향상, 고장률 감소, 다운타임 최소화 등을 위한 의사결정에 반영하는 식이다.
실제 스마트 팩토리에서는 제품수명주기관리(Pruduct Lifecycle Management, PLM) 과정에서 활용 사례가 많다. 제품 개발부터 출하까지 관장하는 PLM은 기업의 전사적자원관리(ERP) 시스템, 공급망관리(SCM) 시스템 등과도 연관된다. 그만큼 활용 무대가 크다는 것이다.
이 시스템들을 통합하는 것이 개념적으로는 쉽지만, 실제로 일관성 있게 통합하는 것은 쉽지 않다. 이 과정에서 디지털 트윈을 활용하면 다양한 가상 객체가 각각의 시스템과 연계해 통합적인 공장 상황을 모니터링하고 표현할 수 있다. 결국 디지털 트윈은 계획·조달·생산·포장·저장·배송 등 제품 전주기에 실질적으로 영향을 미치는 기술로 잠재성이 높다고 평가받는다.
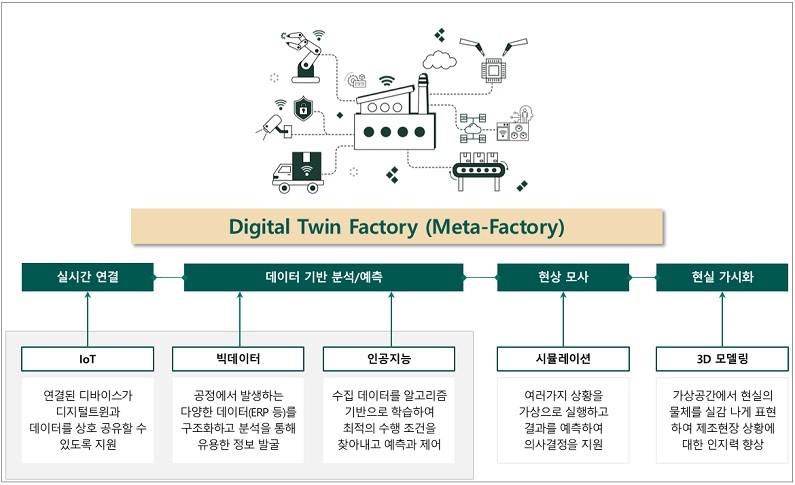
제품 전주기 NO! 공장 전주기로 인식해다오
디지털 트윈은 제품 전주기에 걸쳐 다양한 인사이트를 제시할 수 있다. 이에 더해 품질·설비·안전·환경·에너지 측면의 관리 영역에서도 활용 가능하다. 가상공간에 실제 공장을 구현할 수 있기 때문에 제품 측면에만 국한되지 않는다.
스마트 팩토리는 IT(정보기술)와 OT(운영기술)이 융합된 시스템을 통해 수많은 데이터를 수집한다. 이 데이터를 디지털 트윈 플랫폼과 연계해 가상공간을 구축한 후 설비 유지관리, 자산 관리, 에너지 관리 등을 수행할 수 있다. 이 관점으로 보면, 디지털 트윈은 기업 및 공장 운영자 입장에서 통합 운영 센터(Unified Operation Center) 역할을 해야 한다. ERP·MES 등 기존 시스템 대비 가시성이 극대화된 시스템이기 때문이다.
예를 들어 공장 내 설비의 2D·3D 도면, 운영 및 상태 데이터, 전력량 및 전압량 데이터, 온습도 데이터 등 세밀한 부분까지 표현해야 비로소 디지털 트윈의 본질이 구현되는 것이다. 더 구체적으로 들어가 보면, 공정 기술이 발전함에 따라 공장의 셀 조립(생산품마다 다른 공정)이 한 공장에서 이뤄지는 것이 미래형 공장의 모습으로 됨에 따라 이를 구현하는 과정에서 디지털 트윈 기술이 필수적으로 필요하다. 셀 조립 공정을 테스트하는 데만 해도 상당한 자원이 소모되기 때문이다.
이에이트의 디지털 트윈 도입 방안
앞서 디지털 트윈 기술은 현재 동기화 시뮬레이션까지 기술적 진화가 완성됐다고 언급했다. 디지털 트윈 솔루션 업체 이에이트는 디지털 트윈 플랫폼 ‘NDX 프로(NDXPRO)’와 시뮬레이션 소프트웨어 ‘엔플로우(NFLOW)’를 보유했다.
이 중 NDX 프로는 각종 정형 및 비정형 데이터를 수집하기 위한 커넥터를 갖췄다. 객체를 다루는 방식이기 때문에 모든 데이터가 객체 데이터베이스로 이뤄져 있다. 여기에 ‘NDX 비주얼라이제이션(NDX Visualization)’ 모듈을 탑재해 3D 시각화 기술을 제공한다. 실제와 유사한 3D 모델을 제공해 디지털 트윈의 정보를 시각화한다. 이 모듈을 통해 객체를 스캔해 모델링하는 기존 방식에서 탈피해 소모되는 자원을 절감할 수 있다.
이에이트는 이 과정을 좀 더 수월하게 진행하기 위해 이미지 기반 3D 모델링 업체 ‘PIX4D’와 손잡았다. PIX4D의 3D 모델링 기법을 활용해 휴대폰, 드론 등으로 촬영한 이미지로 3D 모델을 만들 수 있다. 이 결과물을 IoT와 연결해 실제와 같은 객체를 가상공간에 구축하게 된다.
이 기술들이 한 데 접목되고 고도화되면 에너지 최적화도 가능하다. 냉난방 공조, 설비 가동 등을 자동으로 수행해 에너지를 절감하는 방식이다. 이것이 바로 스마트 팩토리가 지향하는 완전 자동화 혹은 자율화의 시작점이 되지 않을까.
오토메이션월드 최재규 기자 |